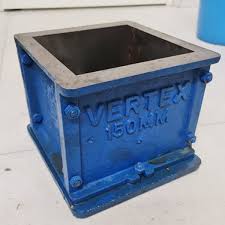
Cube Moulds are essential tools in civil engineering and construction, used for preparing concrete test specimens in the shape of cubes. These cubes are typically subjected to compression testing to determine the compressive strength of the concrete, which is a critical factor in assessing the quality and suitability of concrete for construction purposes.
- Material:
- Cube moulds are commonly made from cast iron, steel, or sometimes plastic, depending on the requirements. The material needs to be durable and capable of withstanding repeated use and the pressure exerted during testing.
- Size:
- The standard size of cube moulds varies depending on regional standards. Common sizes include:
- 150 mm x 150 mm x 150 mm: This is the most widely used size for concrete cube testing, particularly in the UK and many other countries.
- 100 mm x 100 mm x 100 mm: Used in some cases where smaller samples are acceptable, or when the available concrete quantity is limited.
- The size chosen depends on the specific test requirements and standards.
- The standard size of cube moulds varies depending on regional standards. Common sizes include:
- Design:
- Cube moulds are usually designed as a split or two-part mould that can be opened easily to remove the concrete cube once it has hardened.
- They include bolts or clamps to hold the two halves together securely during casting and curing.
- The internal surfaces of the moulds are smooth and well-finished to ensure that the concrete cubes have smooth surfaces and accurate dimensions.
- Base Plate:
- The moulds are typically provided with a base plate, which is also made of the same material as the mould, to ensure the bottom of the cube is flat and smooth.
- Calibration and Standards:
- Cube moulds are manufactured to strict dimensional tolerances to meet industry standards, such as ASTM (American Society for Testing and Materials), BS (British Standards), or IS (Indian Standards). This ensures consistency and accuracy in test results.
- Preparation:
- The mould is cleaned, assembled, and lightly coated with a release agent to prevent the concrete from sticking.
- Fresh concrete is poured into the mould in layers, with each layer being compacted either manually with a tamping rod or using a vibrating table to remove air bubbles and ensure uniform density.
- Curing:
- After filling, the top surface of the concrete is leveled, and the mould is left undisturbed to allow the concrete to set.
- Once the concrete has set, the mould is removed, and the cube specimens are typically cured in a water tank for a specified number of days (commonly 7, 14, or 28 days) before testing.
- Compression Testing:
- The cured concrete cubes are then subjected to compression testing using a compression testing machine.
- The compressive strength of the concrete is calculated by dividing the maximum load applied to the cube by the cross-sectional area of the cube face.
- Quality Control: Used to ensure that the concrete mix meets the required strength specifications before it is used in construction.
- Research and Development: In laboratories, cube moulds are used for developing new concrete mixes and studying the effects of different materials and admixtures on concrete strength.
- Compliance Testing: In construction projects, cube tests are often required as part of the compliance with building codes and standards.
Cube Moulds play a critical role in the testing and quality assurance processes in the construction industry, providing reliable data on the strength of concrete used in various structures.