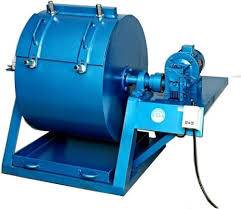
The Los Angeles Abrasion Testing Machine is used to evaluate the abrasion resistance of aggregate materials. This test is critical for assessing the durability of aggregates used in road construction, concrete production, and other applications where resistance to wear and tear is important.
- Drum:
- The machine features a large, cylindrical drum that rotates horizontally. The drum is typically made of steel and lined with a wear-resistant material.
- Internal Lining:
- The interior of the drum is lined with steel balls or abrasive material that impacts the aggregate during rotation. The steel balls help to simulate the abrasive action that aggregates experience in service.
- Drive Mechanism:
- The drum is powered by an electric motor that drives it to rotate at a specified speed. The rotation speed and duration are controlled by the machine’s settings.
- Sample Holder:
- Aggregates are placed in the drum along with the steel balls or abrasive material. The sample holder ensures that the aggregates are evenly distributed inside the drum.
- Measurement and Weighing System:
- After the test, the machine includes a system to weigh the aggregate samples to determine the loss in mass due to abrasion.
- Sample Preparation:
- A representative sample of aggregate is prepared. The sample is typically sieved to a specified size range, usually between 25 mm and 12.5 mm.
- Loading the Drum:
- The aggregate sample is placed in the drum along with a specified number of steel balls (often around 12 steel balls of approximately 48 mm diameter) or abrasive material. The drum is then closed securely.
- Testing:
- The drum is rotated at a speed of approximately 30 to 33 revolutions per minute (RPM) for a set period, usually about 500 to 1000 revolutions, depending on the standard being followed.
- Unloading and Cleaning:
- After the rotation, the drum is stopped, and the aggregate is removed and cleaned to remove any dust or loose material.
- Weighing and Calculation:
- The cleaned aggregate is weighed to determine the amount of material lost due to abrasion. The percentage of loss is calculated using the formula: Abrasion Loss (%)=Initial Weight−Final WeightInitial Weight×100\text{Abrasion Loss (\%)} = \frac{\text{Initial Weight} – \text{Final Weight}}{\text{Initial Weight}} \times 100Abrasion Loss (%)=Initial WeightInitial Weight−Final Weight×100
- Durability Assessment: Evaluates the durability of aggregates by measuring their resistance to abrasion and wear. This is important for ensuring that the aggregates can withstand the stresses they will encounter in service.
- Quality Control: Used in quality control to ensure that aggregates meet the required standards for abrasion resistance, especially in road construction and concrete production.
- Compliance Testing: Helps ensure that aggregates comply with regulatory and standard specifications for abrasion resistance.
- Structural Integrity: Aggregates with high abrasion resistance contribute to the longevity and performance of roadways, concrete structures, and other applications by minimizing wear and maintaining structural integrity.
- Economic Efficiency: Durable aggregates reduce maintenance and repair costs by improving the lifespan of infrastructure and construction projects.
- Performance Prediction: Provides a basis for predicting the performance of aggregates under real-world conditions, helping to ensure that materials will perform as expected over time.
The Los Angeles Abrasion Testing Machine is a crucial tool in materials testing, providing valuable insights into the wear resistance of aggregates and helping to ensure that construction materials meet the necessary durability standards.